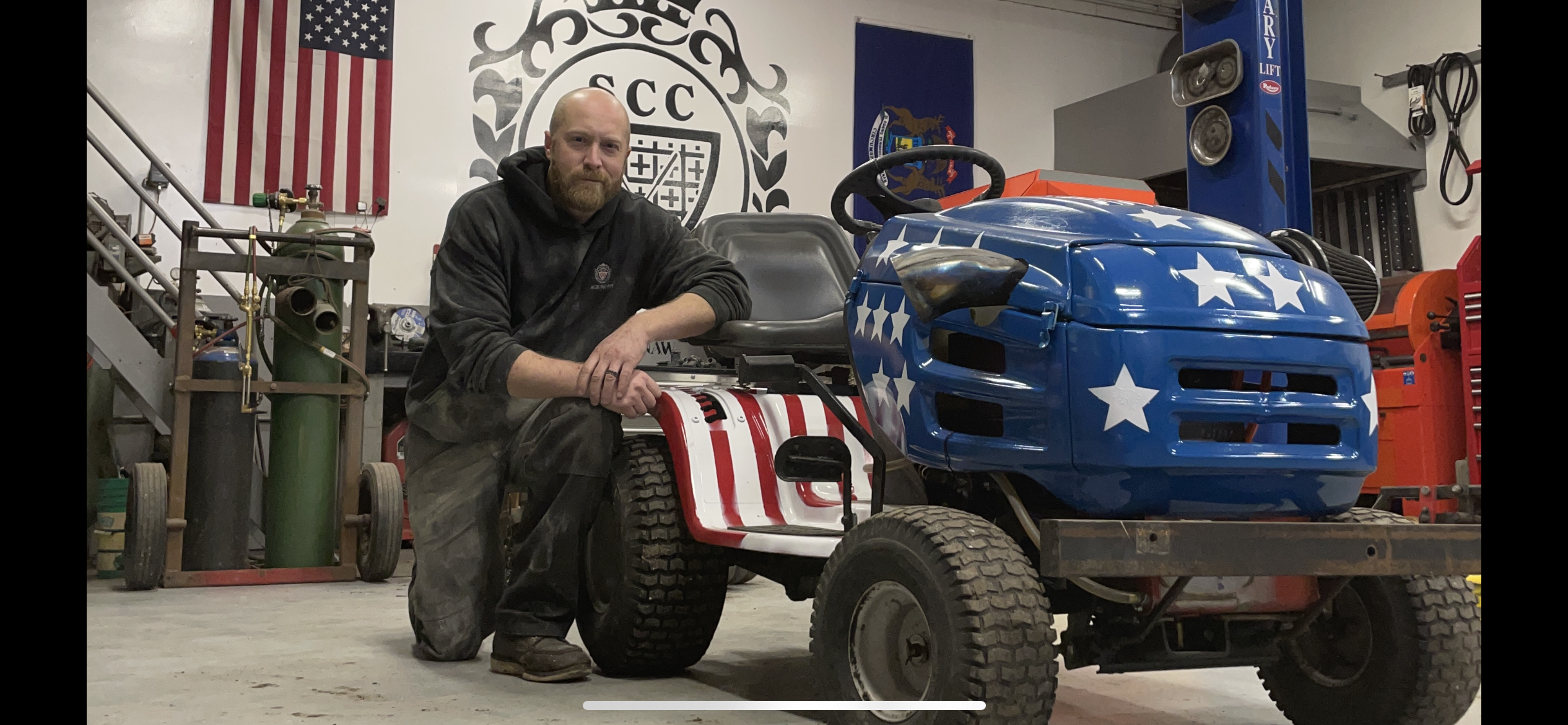
In the spring of 2021, I was invited by a good friend of mine to watch a lawnmower race that one of his acquaintance’s hosts. This really spiked my interest so the following weekend I decided to see what it was all about. I pulled up to the address and was greeted by a 4x8 sheet of plywood that read, “RACE”. The driveway was a rutted up rocky farm trail, that after several hundred yards, opened up to a grassy field that had been turned into a makeshift parking lot. There were several people already there just mingling with one another. The starting line was packed with mowers and the races were about to begin. The festivities lasted until well after dark and it turned out to be one of the most enjoyable events that I had ever attended.
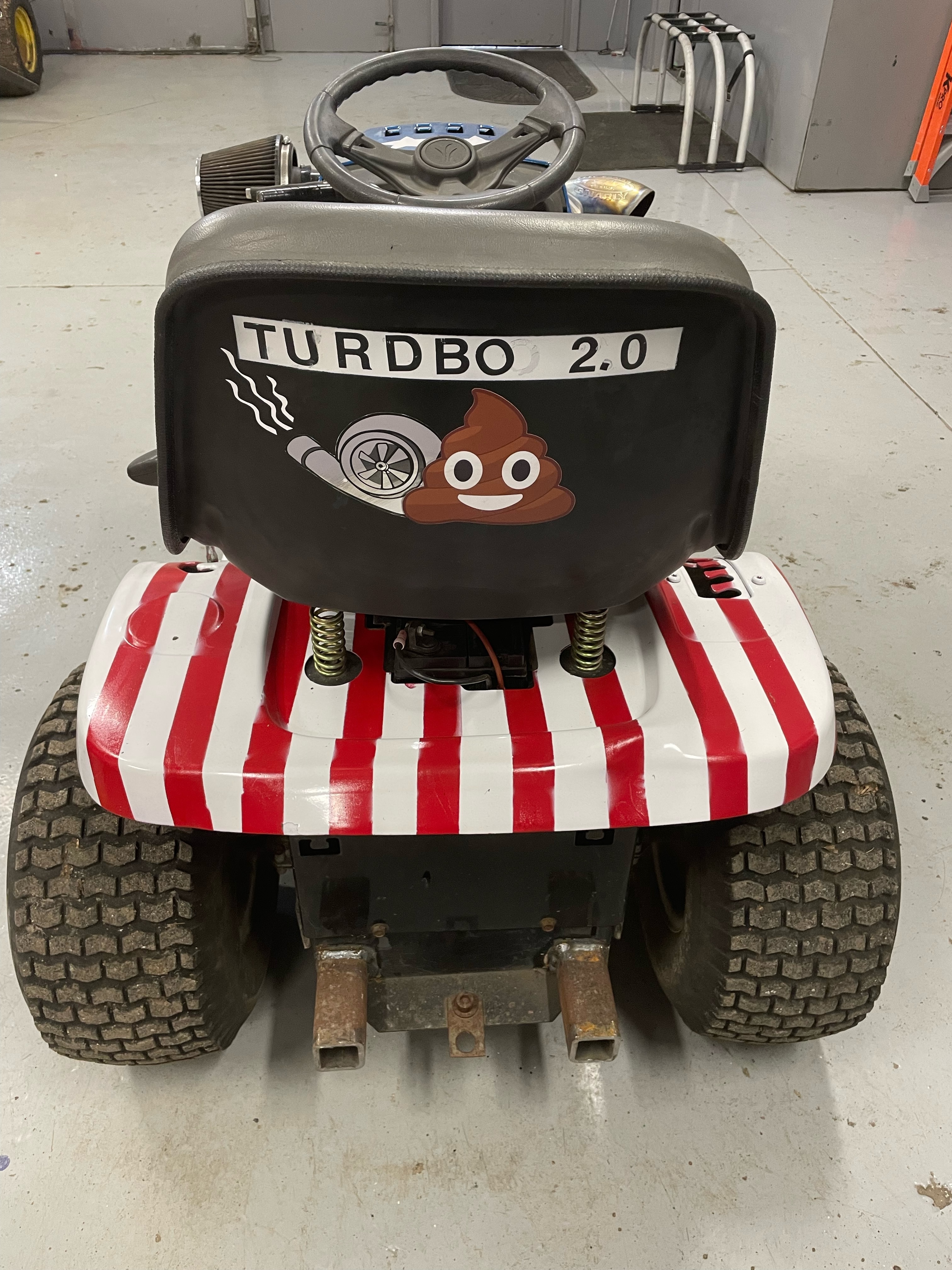
The mowers range from mild to wild. Rattle-can-paint-jobs, tire chains, loud exhausts and crash bars. Since there really aren’t any rules and any real winners or losers, the attraction to me was how ridiculous the mowers could be. Before the races begin, spectators and competitors walk around checking out the mowers as if they were at a car show. Seeing the creativity that went into some of the more elaborate mowers really appealed to me. The custom fabricated bumpers, hand built exhaust systems, body work and paint jobs were so imaginative. The next day I started searching for a mower to enter the race myself. My goal was to build the most outrageous mower they had ever seen.
I decided I was going to design a turbocharged mower, so I started doing research on the subject. I went with a blow-through turbo setup, meaning the carburetor is fed air directly from the cold side of the turbo. This method had one major disadvantage: the pressure differential between the inside and outside of the carburetor. Since carburetors are designed to work off a vacuum and not boost I had to equalize the internal pressures. A modification had to be made to the carburetor bowl by connecting a boost line spliced from the waste gate of the turbo. This modification keeps fuel from leaking past the carb seals and makes tuning much easier. So as to not break the bank, I sourced a cheap vz21 small displacement turbo from eBay for around 120 dollars. I also found the correct flanges and seals for the turbo set-up for about 50 dollars. Since the turbo wouldn’t be intercooled, I decided to use an auxiliary oil tank and pump to circulate oil through the turbo. This set-up would help keep the turbo cool and lubricated instead of relying on the engines internal oil pump. By keeping the engine and turbo oil separate, it eliminates the need for a complicated intercooler set-up. I found a 12 volt viscous fluid pump on eBay for around 70 dollars, which would draw oil from the auxiliary tank through a hose to the turbo. I had everything drawn out in my head, but now I needed a cheap mower to put it on. Next step, score a lawn mower!
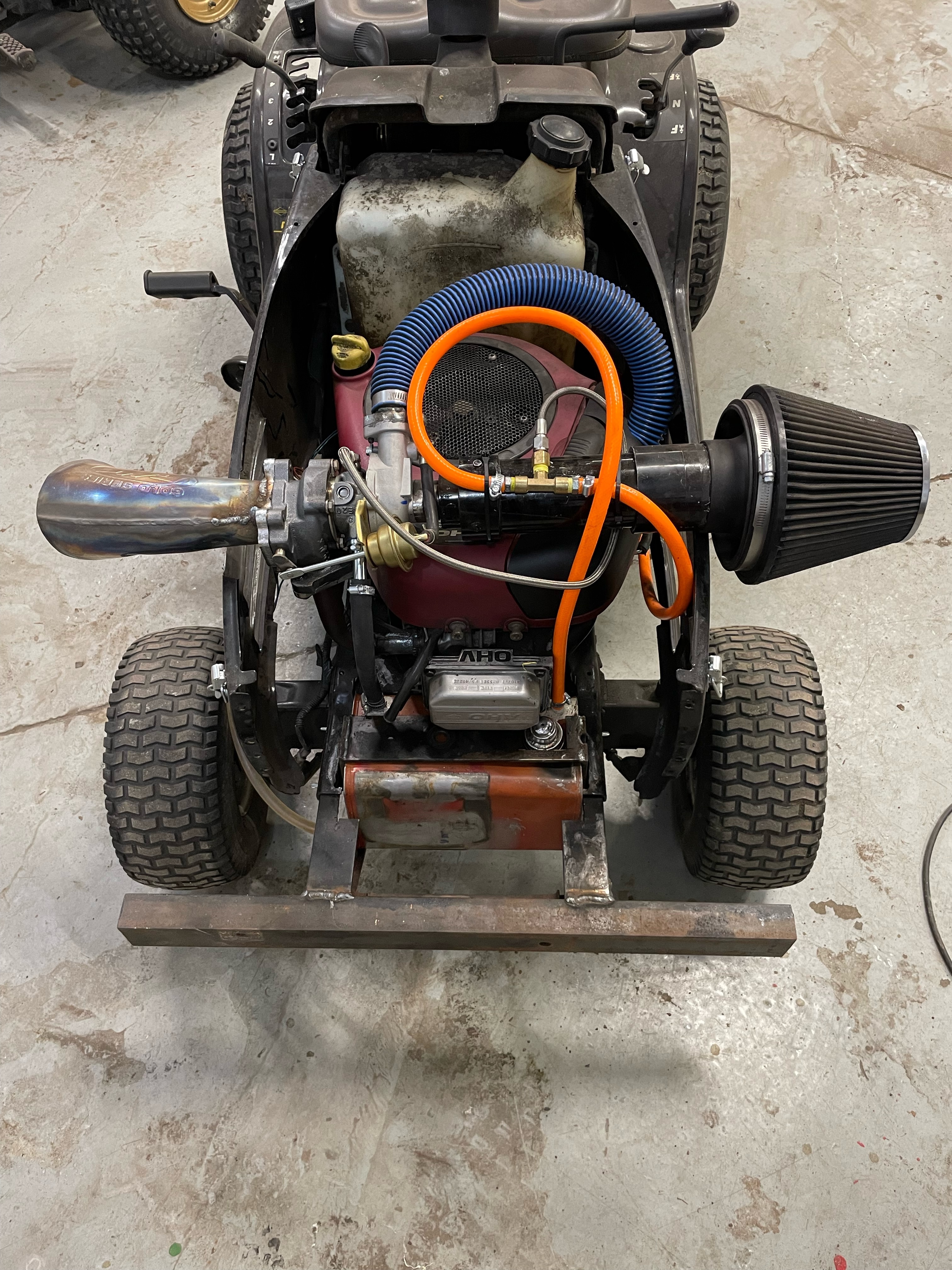
Again, I searched Facebook marketplace for a few days until I found a mower that suited my needs. I found a running driving mower for 100 dollars, the only caveat being that it needed a valve adjustment. After adjusting the valves to spec the engine started perfectly and it was time to start fabricating. I welded up a new exhaust with a flange on the top to accept the turbo. I then mounted a down pipe on the hot side of the turbo which was made from a piece of an old expansion chamber. The cold side of the turbo needed a velocity stack which I made from a piece of 3” pvc and a reducer. The end of the pvc was fitted with an oversized K&N air filter. With the turbo installed, my next step was to plumb the auxiliary oil tank and pump. The oil tank was simply an old lawnmower fuel tank fitted with multiple barbed fittings. I then mounted it to the lower front end of the mower directly under the turbo, so that gravity would return oil to the tank after being pumped through the top inlet. A splice had to be placed in the line before the inlet to allow excess pressure from forcing oil through the seals of the turbo and burning off through the exhaust. This process continuously circulates oil, dissipating heat and keeps the turbo lubricated. Now for the fine tuning...
Ironically, tuning the engine proved to be the most challenging and time consuming part of the whole process. I’m no expert, so lots of trial and error was needed. It wouldn’t hurt to learn how to read a spark plug either. The jetting in the carburetor needed to be changed several times until I found the perfect setting. Once the correct jetting was achieved and the mower was running good, it was time to make it faster!
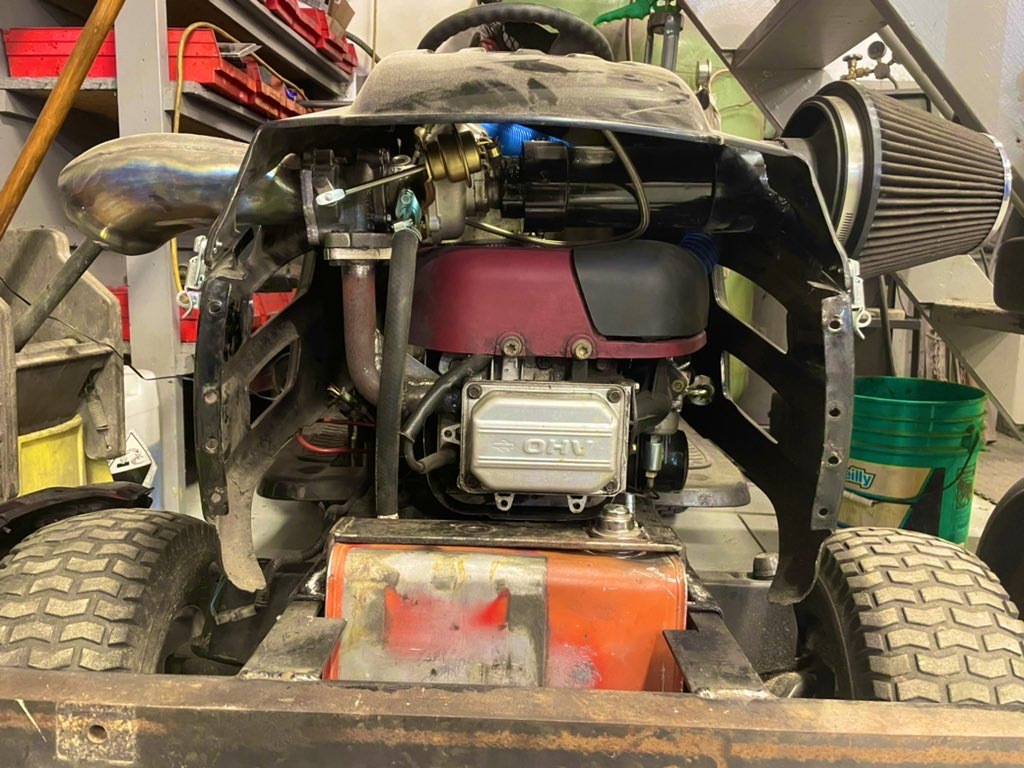
Although I wanted the mower to be fast, it still needed to have enough torque to climb muddy hills and navigate rough terrain. I changed the transaxle pulley size by 1.5 inches and experimented with several belt sizes, until I found a combination that wouldn’t slip. After test driving the mower and finding a happy medium of speed vs torque, it was time to add bumpers as racers offer crash into trees and one another. Since my auxiliary oil tank was on the front of the mower, it became very important for the for it to be protected. I welded a couple pieces of angle iron to the frame and added a solid steel bar across the front. Not only did this bar protect the oil tank, it also put weight over the wheels making steering much more responsive. Now it’s time for an eye catching paint job.
I had the color scheme picked out before I even purchased the mower. As a proud American, it had to be a “Stars and Stripes” design, so I went to the store and snagged some red, white and blue spray paint. I pulled each body panel off individually and used masking tape to create the stripes and stars. The end result turned out great and mower looks amazing, considering I’m not a very talented painter.
I am the kind of person who takes my work home with me whether it’s negative or positive. As an equipment manager you can’t control what breaks or when, nor can you estimate the ease or difficulty of the repair. In any case, it proves to be a stressful job with many highs and just as many lows. Engaging in a positive activity can help alleviate daily stress and anxiety, this is why having some kind of hobby is so important. My hobbies happen to mimic how I make a living, but without the time restraints. I set my own priorities and can step away from projects as I see fit.
Overall the build proved to be a fun stress release for me and is in no way perfect, but an invaluable learning experience. The knowledge I’ve gained by experimenting on cheap lawnmowers will help me on future large scale projects and add to my collective mechanical skills. A great stress release with an even greater ride ahead. Meet you on the starting line!